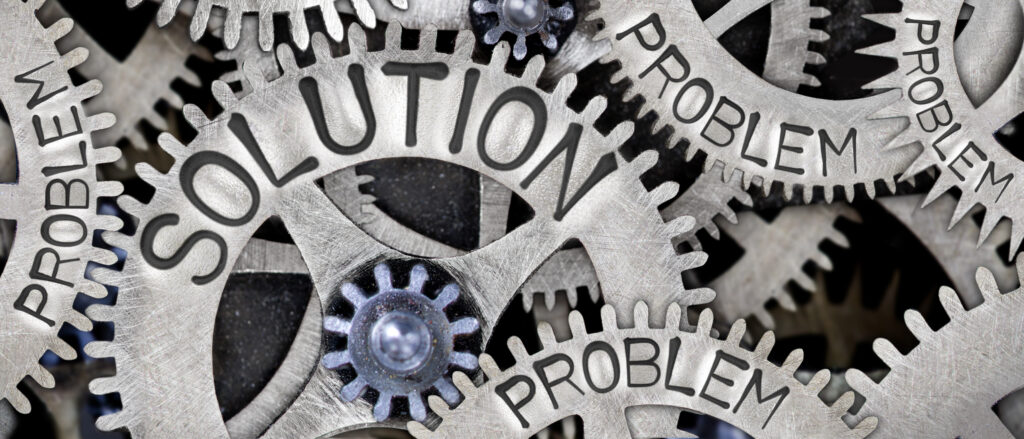
The shrink sleeve labeling machine is used for the back-end packaging of a production line and is used in various industries, such as the packaging of bottled water, beverages, daily chemical products, and the pharmaceutical industry. The technology of the sleeve labeling machine made in China is already very mature, and the operation is relatively simple, but as long as it is a machine, there will be some small problems sometimes.
Here are 9 faults you might meet, together with the Solutions for each fault.
- Shrink labels show cracks and wrinkles
- Labels accumulate or get stuck on the center guide column
- The cut position of the label is uneven and has burrs
- Many labels do not drop into the bottom of the bottle:
- Large numbers of labels miss the bottles
- Consecutive delivery of many labels while passing a bottle
- Label sizes are always cut incorrectly
- Machine cutters are extremely easy to break
- The blade cuts to the center column and the blade breaks
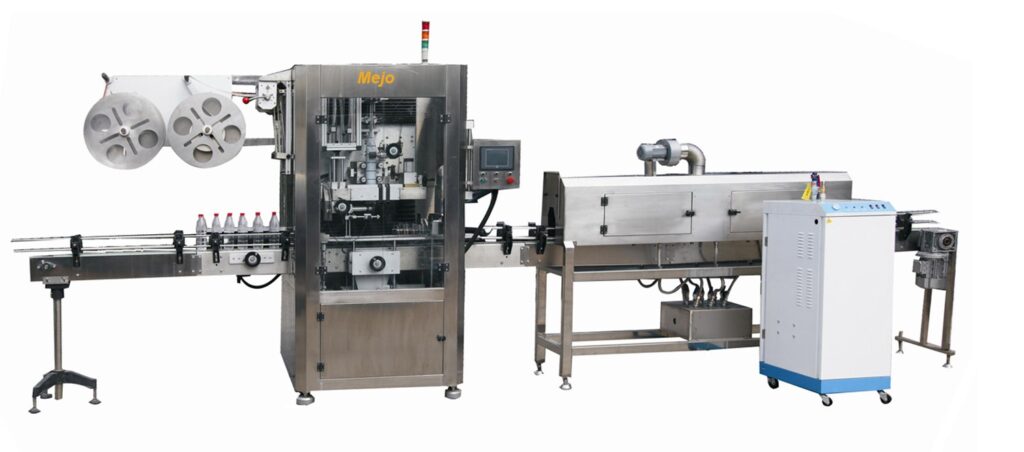
1. Shrink labels show cracks and wrinkles
Reason:
- Blowing ports in the shrink tunnel are not adjusted properly, and the temperature in the shrink tunnel is too high or too low
- When the shrink label comes into contact with the surface of a cooler container (such as a carbonated beverage, which is filled at about 4°C), cracks and wrinkles can appear on the container because the changing temperature slows the shrinkage process.
- The shrinkage of the label is not stable.
- Conveyor belt speed varies frequently (it is the variation in conveyor belt speed that decides the time the bottles stay in the shrink tunnel).
Solution:
- Change into a label material with a better shrinkage rate, for example, if you are using PVC, you need to change into PET material now
- The speed of the conveyor belt is suggested to run at the biggest production line speed and it is recommended not to adjust it frequently.
- Adjust the proper position of the blowing ports to the most propitiate positions.
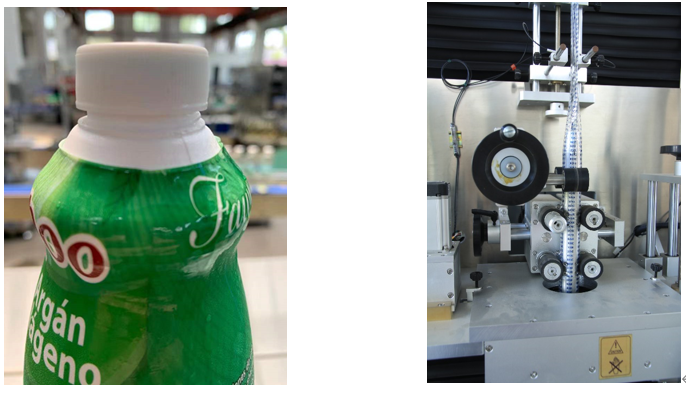
2. Labels accumulate or get stuck on the center guide column
Reason:
- Shrink labels are partially shrunk during transportation or improperly stored, resulting in a smaller label size.
- The clamping point of the central guide column is also more likely to result in unstable clamping, so that the central column cannot become a line, resulting in material accumulation.
- The adjustment strength of the upper and lower drive rubber wheels is inconsistent.
- When the edge of the cutter returns to the origin every time it rotates, it may stop in the groove of the center column, which makes the film label touch the blade and results in material accumulation.
- The groove of the center column may be “cut” by the cutter, which will cause the subscript to be unsmooth and cause the material to jam.
- When the cut label is waiting to be brushed off, the brushing wheel does not smoothly insert the cut label into the bottle body, resulting in a domino effect, which makes the central column accumulate labels.
- After the new blade is replaced, the length of the blade is not enough to cut off the label,
and then it cannot be brushed and inserted and the material will be stuck.
Solution:
- The label diameter value should be within the ±0.5% error range. The thickness of the small label is not less than 0.035mm, and the thickness of the big label is not less than 0.045mm.
- Correctly adjust the strength of the upper and lower driving rubber wheels.
- Check whether the origin point of the cutter is correct, and check the matching of the whole process control. Be sure to drive the next piece of label within the effective time after the cutter leaves the center column. In addition, the cutter should stay inside the cutter head every time it stops, and it should not be too close to the groove of the center column, to ensure that no label is accumulated.
- If there is a cut in the groove of the central column, just smooth the surface.
- Make sure that all the blades have the same length after the replacement and can just cut off the label, please refer to the old blade before replacement.
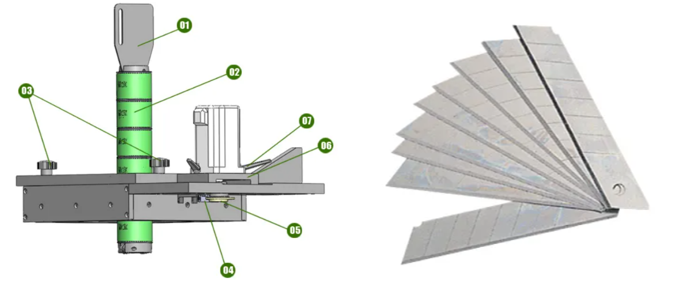
3.
The cut position of the label is uneven and has burrs
Reason:
- The label is too large, and the deviation between the diameter of the center column and the folding diameter of the label is too large.
- leveling point of the cutter box is not on the line.
- Inside the cutter box group, the gap between the groove of the eccentric shaft and the bottom of the cutter seat is too large, which makes the blade uneven.
- The blade is not strong enough.
- The position of the center column is not installed correctly
- The blade is not locked and slips off during operation, making the blade break.
- The replaced blade was too long and touched the center guide column.
Solution:
- Do a good job in the control of the label size, and confirm that the label folding diameter matches the diameter of the center guide column.
- Confirm the flat point after blade replacement and tightness control of the lock blade.
- Just replace the relevant parts inside the cutter set.
- Replace with a new blade.
- Regularly check whether the screws inside the cutter head group (such as the bottom of the cutter seat, the cutter seat, the tired thread of the cutter seat cover, etc.) are loose or not.
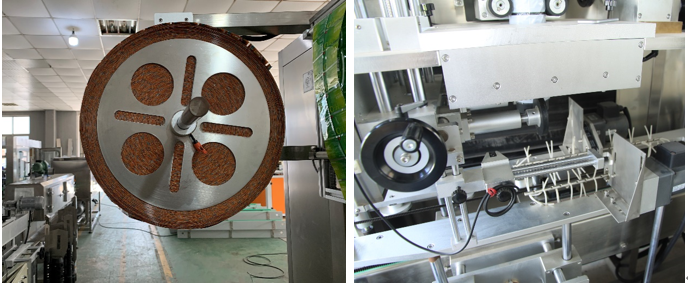
4.
Many labels do not drop into the bottom of the bottle:
Reason:
- Too much water on the bottle.
- Too few brushes.
- The brush wheel falls to the bottom of the center column, which makes the label not round when dropping.
- The lower wheel is clamped too tightly, which makes the label deformed.
Solution:
- Add a water blower before entering the sleeve labeling machine, or replace the present one with a more powerful one.
- Increase the number of brushes.
- Adjust the wheel which brushes down the labels.
5. Large numbers of labels miss the bottles
Reason:
- The bottle and the central column are not inline
- The center guide column is not fixed, and it shakes when the machine is turned on
- The position of the electric eye of bottle detection is not adjusted properly
Solution:
- Adjust the center guide
- Adjust the electric eye of bottle detection.
6.
Consecutive delivery of many labels while passing a bottle
Reason:
- The supporting shrapnel in the lower section of the central guide column is loose or broken.
- Abnormal signal of the Photoelectric eye of the bottle detection.
Solution:
- Replace the shrapnel with a new one and adjust it to properly stretch the label.
- Adjust the sensor position or sensitivity of the sensor.
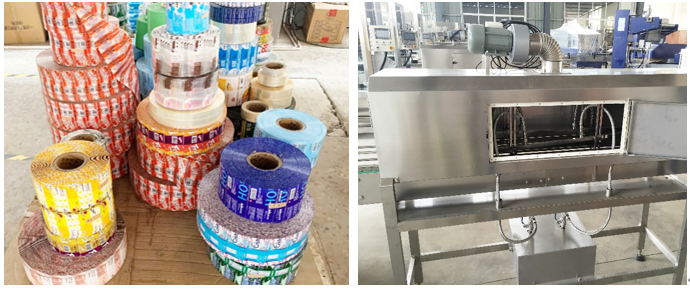
7. Label sizes are always cut incorrectly:
- The segmented electric eye is too dirty
- The sensor sensitivity is not adjusted well.
- The parameters in the PLC are not adjusted properly
- Drive belt is loose
8.
Machine cutters are extremely easy to break:
- The origin of the cut point is not positioned well.
- The center column drive wheel is not fixed well.
- When the label is stuck, the inner label of the cutter head is not cleaned up
- The machine is not shutting down in time when the label is stuck.
- The blades are not incorrectly installed.
9.
The blade cuts to the center column and the blade breaks:
Reason:
- Maybe the center guide column is not properly installed, which makes the center column slide down during the sleeve labeling process, and the blade cuts to the center column and breaks the blade.
- Maybe the blades are not locked well and slipped during operation, which makes the blades break.
Solution:
- Install the center guide column correctly.
- Regularly check the screws inside the cutter head group ( such as the bottom of the cutter seat, the cutter seat, the thread of the cutter seat cover, etc.)
Itís difficult to find knowledgeable people in this particular subject, however, you seem like you know what youíre talking about! Thanks
thanks so much! friend.
For your appreciation and kindness!
are you also in this business?
my whatsapp is: 0086 13776250797
welcome to add me there and communicate!
thanks so much!
we will work harder to improve our articles with videos!
I need to to thank you for this very good read!! I certainly loved every little bit of it. I have you book-marked to check out new things you postÖ
thanks so much for your appreciation! friend. so, you are also interested in building a bottled water production line?